crafts
manufacturing secrets
From the Paris workshop to the Limoges factory

Porcelain is the noblest and whitest ceramic paste in existence: it is also called white gold or the queen of ceramics. It is the most timeless and refined of all materials, historically used for royal services. Thin and translucent, yet resistant to everyday use, it withstands the rigors of the microwave, oven and dishwasher.
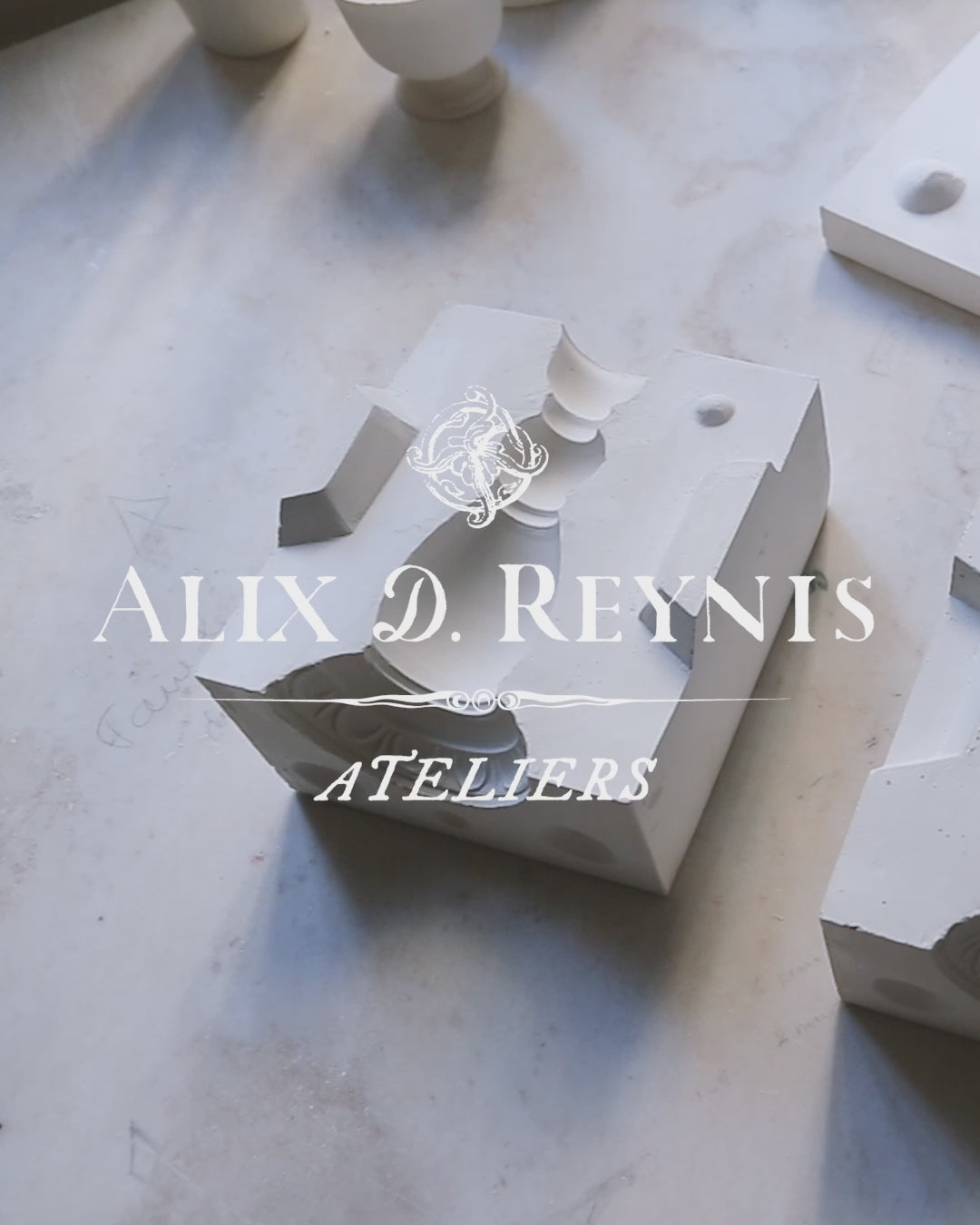

IN THE PARIS WORKSHOP
The story of our pieces begins in the heart of our boutique-atelier in Saint-Germain-des-Prés, where ideas come to life and the entire preliminary phase of creation takes place. Once the inspiration has been found, the creation of a model always begins with a drawing of the imagined piece. Design then begins on a plaster lathe. When the shape is ideal, the motifs, if any, are engraved: the model is finally ready.
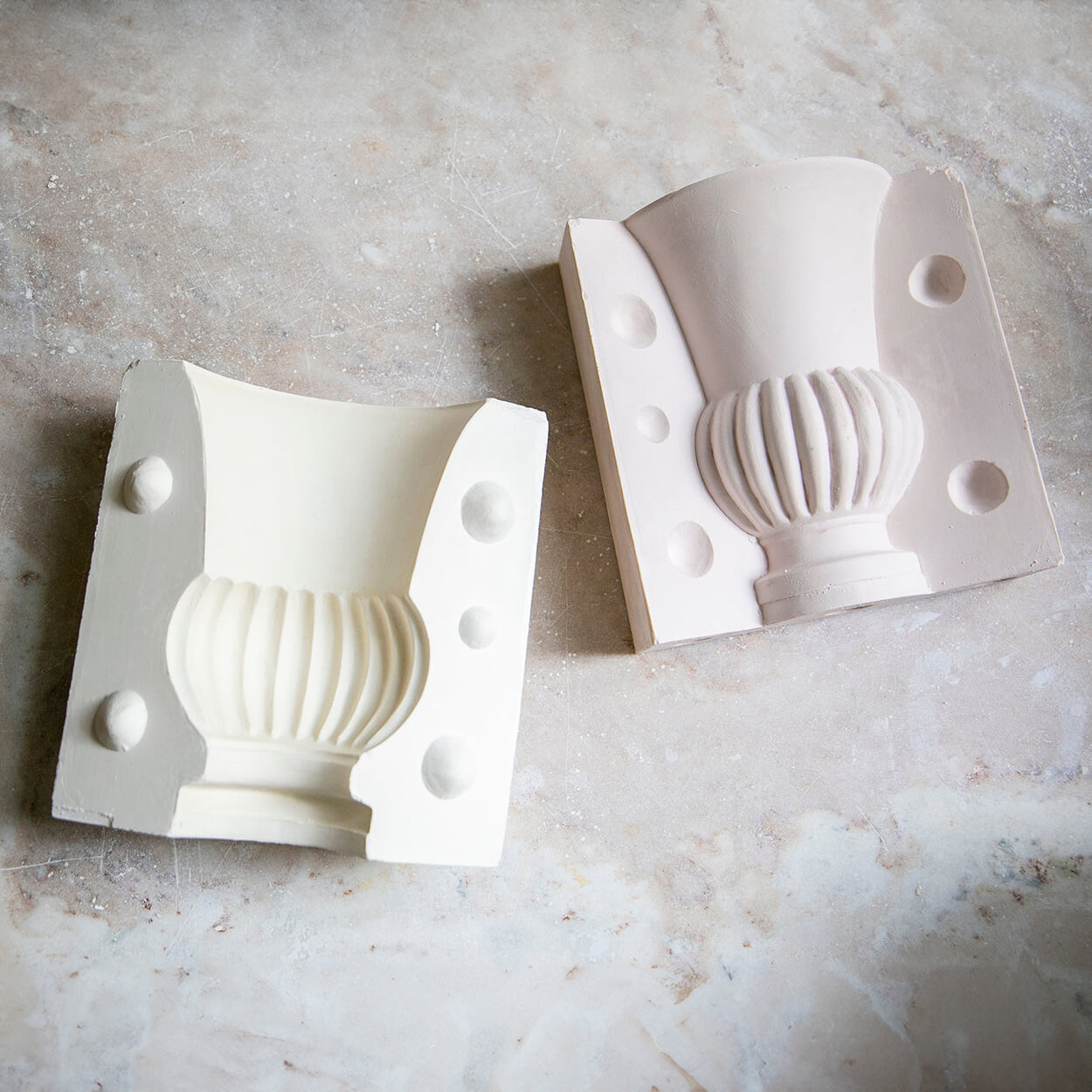
Our pieces are handmade but mass-produced, so a mold must be made from the model and sent to the factory. Once the model is completely dry, it can be molded. Once the first mold has been made, it is sent to Limoges to validate the design. Once this prototype has been validated, the Paris workshop can get down to making the matrix, also known as the “mold mother”.
The matrix, also known as the “mold mother” or “mold of the mold”, is used to generate several molds, each of which has a limited lifespan (around 40 parts). It can be made of plaster or silicone. The manufacturing molds, cast in plaster from the matrix, are then used by the factory to make all our porcelain pieces.

AT THE MANUFACTURE IN LIMOGES
The pouring process
The porcelain casting stage takes place in Limoges, using traditional techniques. For each piece, the mold is closed, then filled to the brim with liquid porcelain. The craftsman then waits for the plaster to absorb the water from the porcelain. The mold is emptied as soon as the porcelain has reached the required thickness: it then remains coated on the mold walls. Once this porcelain crust has hardened, the piece is removed from the mold, then dried completely outside the mold.
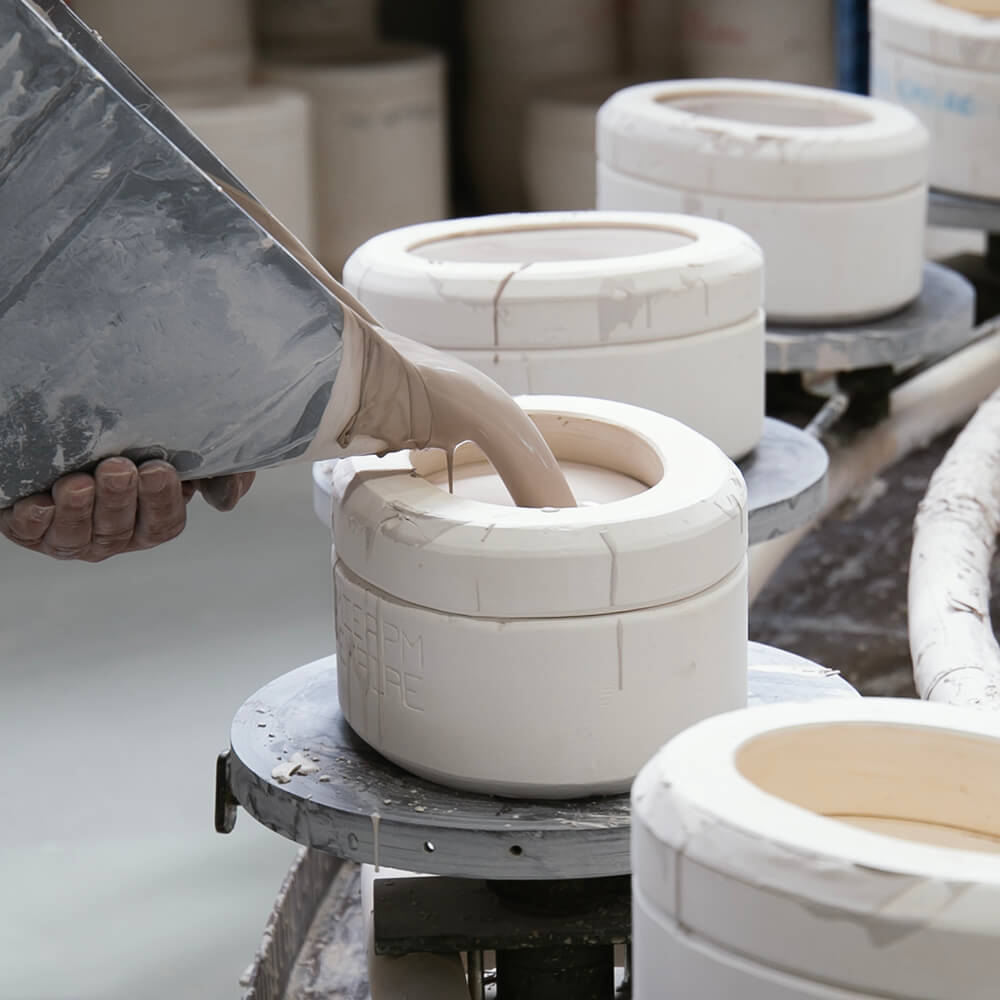
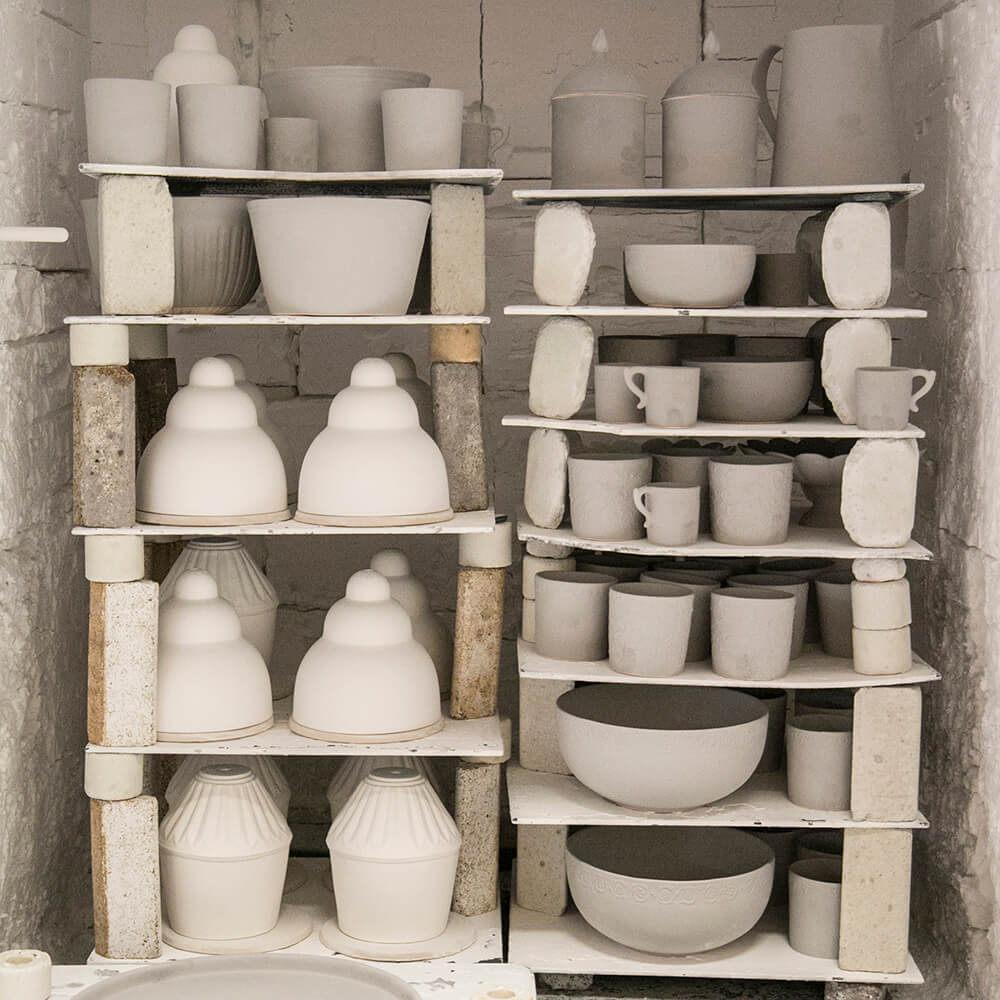
Drying and firing
Before firing, the pieces are dried. This drying stage allows the water contained in the paste to evaporate completely. Porcelain then requires several firings. The first firing is at 980°, known as the “dégourdi” firing. They may or may not be glazed, and are then fired again at a high temperature, 1400°. It is at this temperature that porcelain reveals its transparency, whiteness and strength. Between the first and second firings, the pieces can be glazed: one by one, they are dipped in a bath of glaze that gives the porcelain “cookie” its glaze and shiny appearance. Our factory uses the dipping technique for this step.

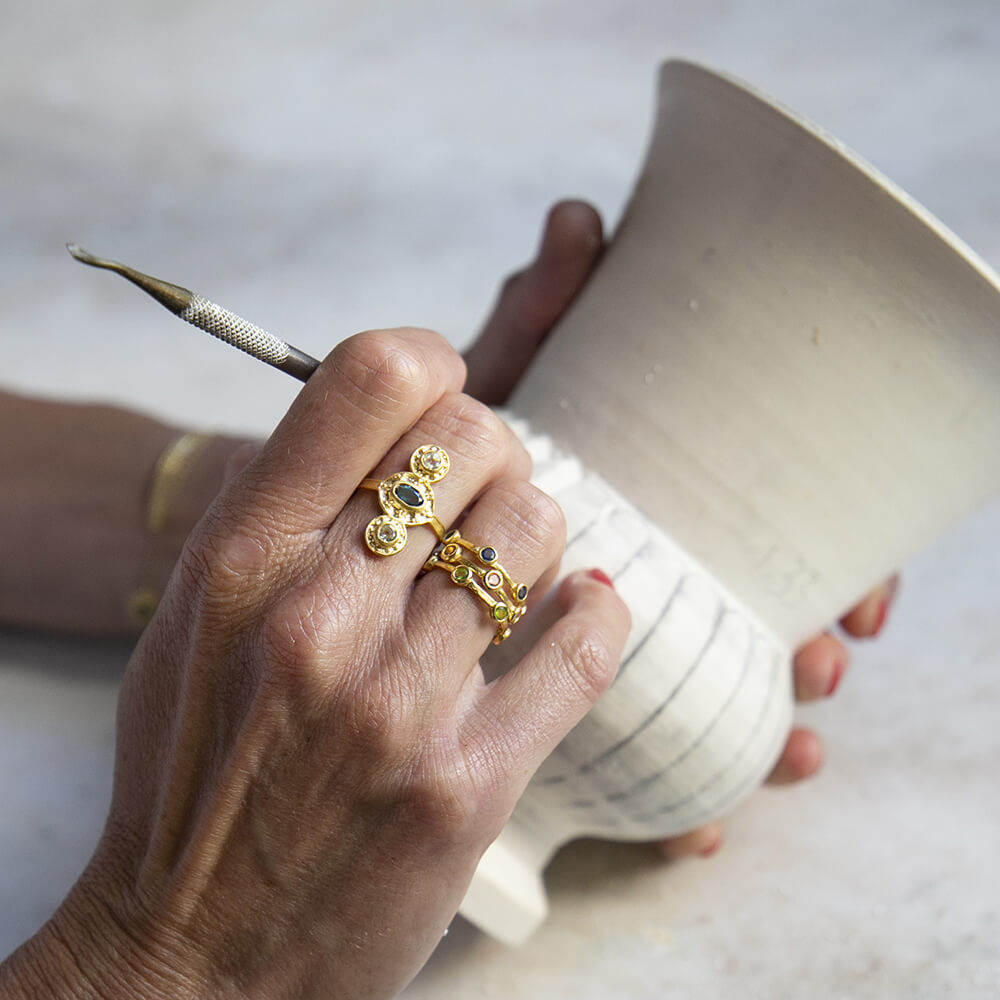
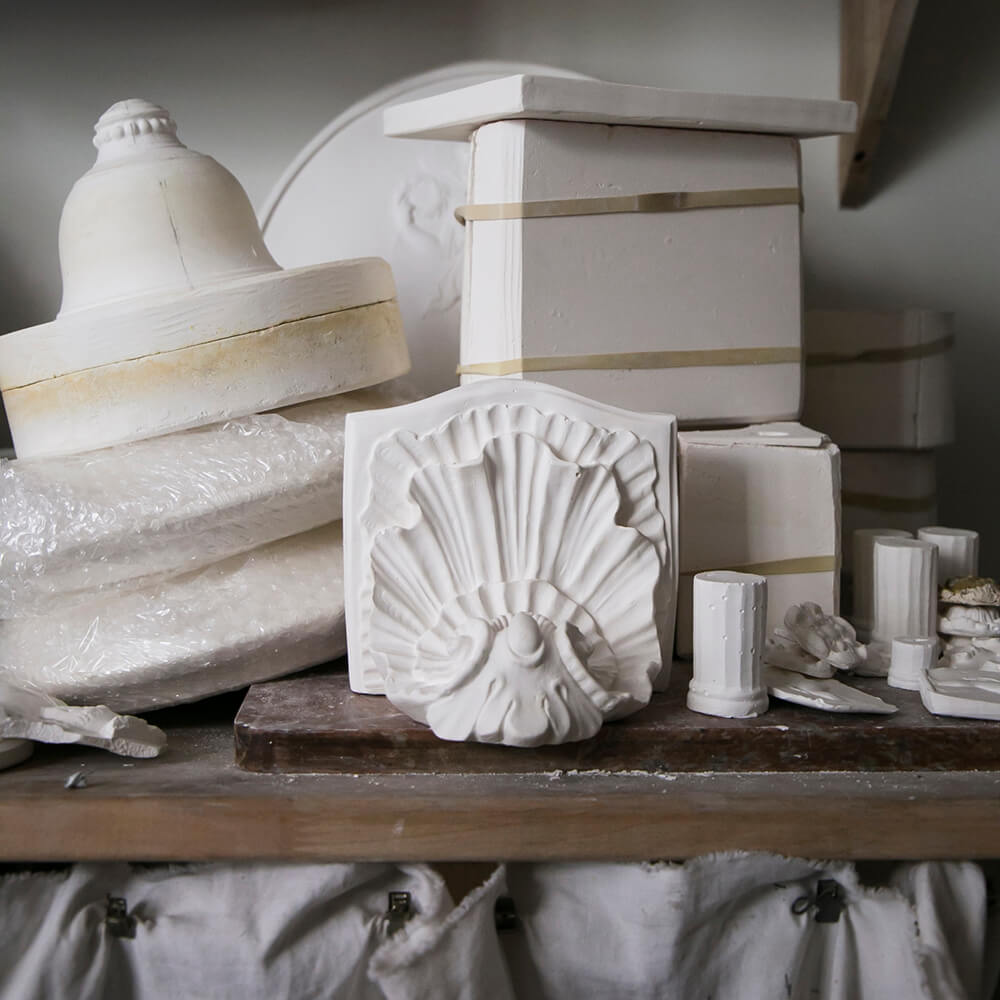
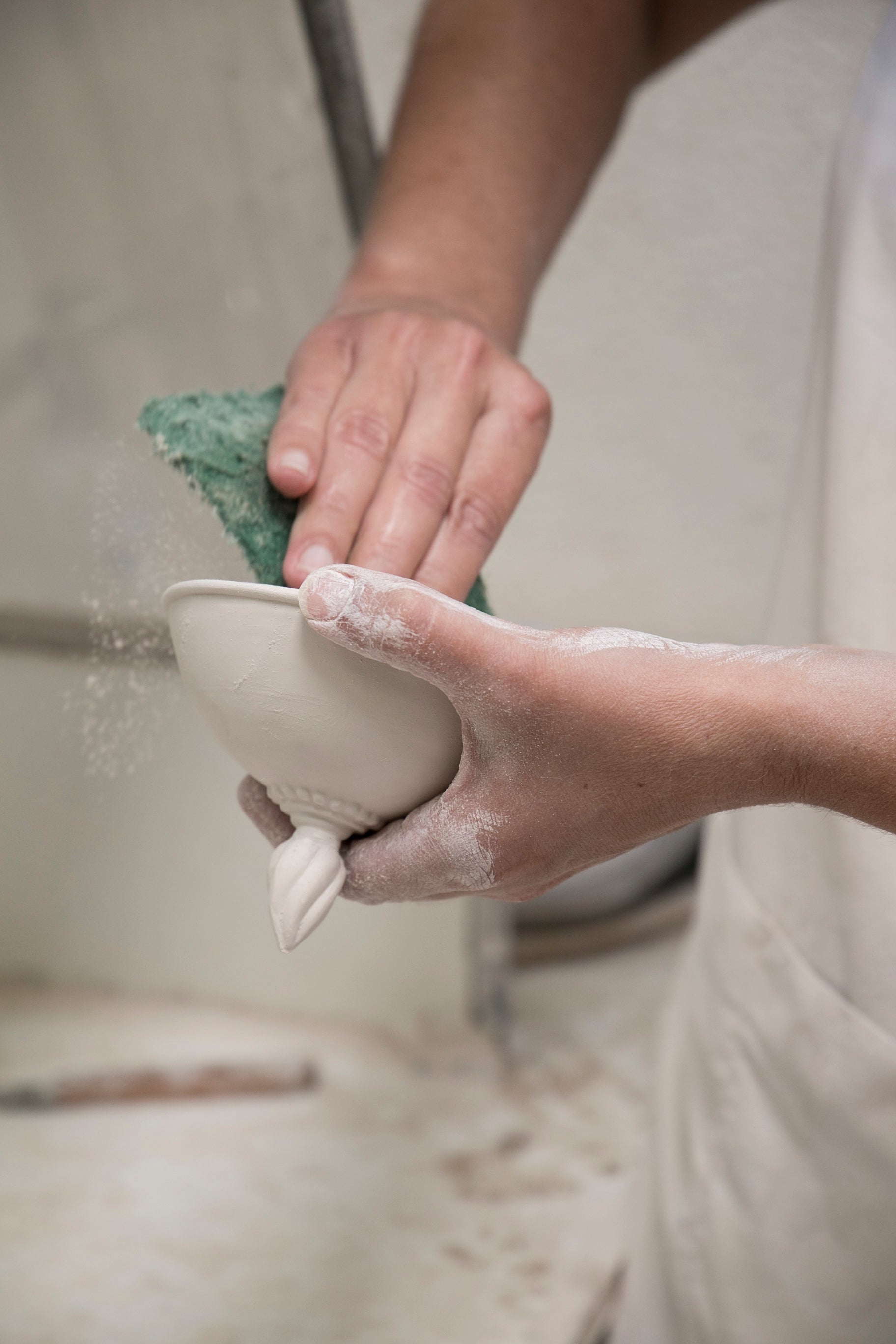
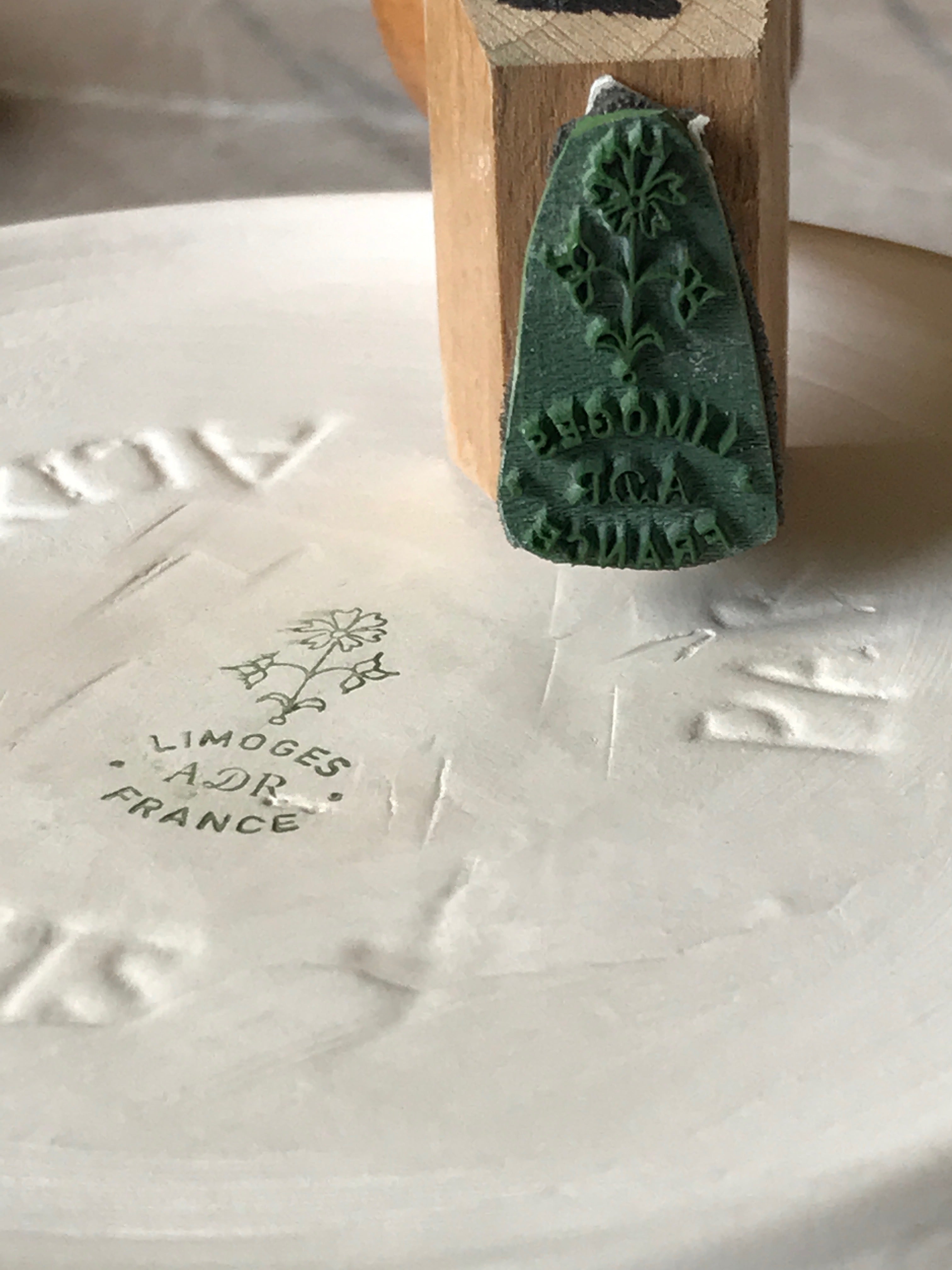
